3,4 and 5-Axis Precision Milling
Datum Tech has both simple and complex CNC Vertical milling and 5 Axis milling capabilities. The orientation of the spindle is the most fundamental characteristic of a machining center. Vertical machines are generally favored for the higher precision parts we typically do. Higher speed throughput, more precise cutting angles and the ability to program automatic tool changes and optimal tool paths enable us to create even the most challenging geometries.
Our work for aerospace, electronics and medical manufacturers relies heavily on the ability to hold very tight tolerances, and to mill unique geometries or cavities in a wide variety of materials ranging from very hard materials like titanium or tool steels to softer metals and plastics.
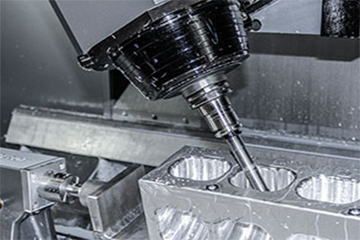
Y-Axis, Live-tool Turning
In addition to common turning or lathe processes, we also employ Live-tooling. This improves workflow for complex parts that require more complex geometries that would otherwise require multiple machines and setups. Live-tooling is essentially the integration of milling and turning operations on the same machine, in this case with sequential processes. But, by adding a third linear axis to the turning-center turret (a live Y-axis) this enables the rotary cutters to machine across the spindle center line.
Rather than take a turned part to a second machine tool when it needs a slot milled or a hole drilled, with live tooling we can do simple milling, drilling, and tapping, right on the turning center. This saves work and cycle-time, and that allows us to save money for our customers.
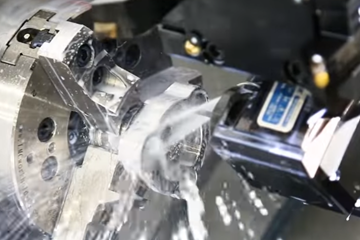
Swiss Turn, Small Parts
Developed many years ago for the Swiss watch-making industry, Swiss-type turning is designed to turn small, complex parts with high precision. Bar stock is fed from a feeder, and we typically handle up to an inch or more of diameter. CNC controls allow simultaneous processing with multiple tools (milling and drilling) and 7 (or more) axes of control.
In the Z axis, the tool is stationary and the stock advances from the main spindle through a guide bushing to expose only the length to be machined - this eliminates vibration and enhances precision. The bushing and, when necessary, a sub-spindle, clamp the stock properly to minimize deflection. Meanwhile, the machine's Y axis does the milling. With proper setup, materials and tooling, Datum uses this capability to hold .0001 in. tolerance on very small parts
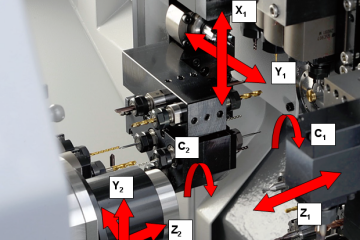
Prototyping - Tool Making
Datum Technologies has dedicated rapid prototyping (R&D) cells (turning, milling and CMM) for the express purpose of getting your designs to First Article in the shortest time possible, in-spec and on budget. Especially for capital equipment makers, semiconductor, medical, aerospace and electronic test instruments - we realize that your time-to-market depends upon our faithful reproduction of your newest concepts and drawings - and protecting your proprietary content.
Datum's highly skilled tool-makers have years of experience building Jigs, Fixtures, Dies, Molds, Machine Tools, Gauges and other Tools used in the machining process. Often, the sophisticated 'multi-axis' or 'done-in-one' machining processes used (above descriptions) rely on fixtures or tooling that enable them to produce higher-accuracy, complex parts in fewer setups - saving time and money.
